
Oxy Cutting
Robinson Metal Recyclers employs a team of highly skilled and experienced oxy cutters. Using industry-leading technology, our team works on-site to dismantle large metal equipment and structures to prepare them for processing.

What is Oxy Cutting
Oxy cutting is a fast and efficient method of cutting scrap metal and is used to cut a wide range of metal types including steel, manganese and high-carbon steel such as rail. This method is commonly used in scrap metal recycling to separate metal into smaller pieces for further processing and is used to cut a wide range of metal types including Steel, Manganese, and High-carbon steel such as rail.
Oxy cutting uses a mix of oxygen and fuel gas to make a high-temperature flame. We use Liquified Petroleum Gas (LPG) because it's better suited to industrial metal recycling and cuts better than other gases. This flame is directed at the material being cut, melting it and allowing it to be separated into two pieces. The high-temperature flame also sterilises the metal, making it safe for further processing.
The oxy cutting process involves the following steps:
Pre-treatment:
Before cutting metal, other methods typically need to clean and prepare the surface by removing paint, rust, and other contaminants. But with our state-of-the-art cutting torches, those things don't slow us down – less preparation means much quicker project cutting times.
Set up:
The cutting equipment, consisting of a cutting torch, oxygen supply, and fuel gas supply, is set up and connected to the metal piece.
Ignition:
The cutting torch is ignited to produce a high-temperature flame by mixing the fuel gas and oxygen in the torch.
Cutting:
The flame is directed at the metal piece, heating it to its melting point. The oxygen in the flame reacts with the metal, producing molten metal and oxides. The pressure of the oxygen pushes the molten metal away from the cut, separating the metal into two pieces.
​
Repeat:
The cutting process is repeated as needed to separate the scrap metal into smaller pieces for further processing
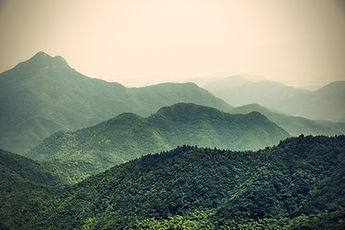
LPG Fuel for Oxy Cutting
Our oxy cutting specialist use Liquefied Petroleum Gas (LPG) as a fuel for the oxy cutting process. LPG offers a high heat output resulting in faster and cleaner cutting through the thickest and hardest of metals.
LPG as a fuel in oxy cutting provides several benefits, including:
Clean burning:
LPG produces fewer pollutants compared to other fossil fuels, making it a cleaner option for oxy-fuel cutting.
​
Portability:
LPG is stored in small, portable containers, making it easy to transport to remote cutting locations.
Ease of use:
LPG is easy to ignite and regulate, making it simpler and safer to use.
Cost-effective:
Compared to other fuels, LPG is relatively cheap and readily available, making it a cost-effective option for oxy-fuel cutting.
On rare occasions we might use thermic lances but in the majority of cases we use our state-of-the-art Oxy-LPG cutting torches which do the job in less time and provides improved productivity.
Benefits of On-site Oxy Cutting Services
Our on-site oxy cutting service is tailored to your timelines, budget and business requirements. Here are just a few of the benefits of using Robinson Metal Recyclers for your operations’ on-site metal cutting and oxy cutting services.On-site oxy cutting offers:
Increased Efficiency:
Allows scrap metal to be processed and cut into smaller pieces as on-site, eliminating the expensive cost of onsite cranes and oversized transport and permits.
​
Improved Safety:
Lowers the risk of accidents during transportation and reduces the exposure of workers to hazardous materials and waste.
Reduced Waste:
Reduces the amount of waste generated during the cutting process, as any generated waste can be set aside for recycling or be disposed of immediately on site.
​
Improved Quality:
Allows scrap metal to be cut and processed to meet specific size and shape requirements, improving the quality and value of the final product.
Increased Flexibility:
Allows scrap metal to be cut and processed according to specific customer needs and demands, increasing the flexibility and responsiveness of the recycling operation.
​

